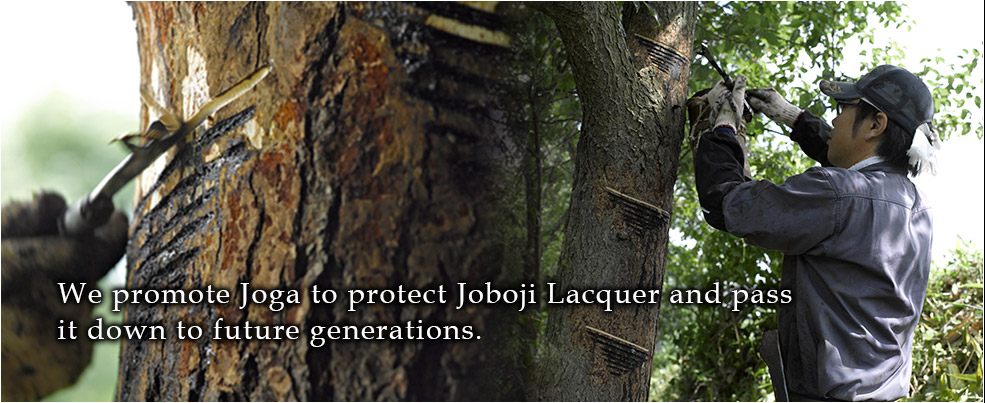
What is urushi?
Urushi, also known as Japanese lacquer, is a natural resin-based paint and is mostly made up of a substance called urushiol.
Urushi lacquer is most commonly used as a coating.
Utensils coated with urushi lacquer are called lacquerware.
Urushi-lacquer coating, characterized by its glossy black appearance, has been recognized as a traditional craft for its beauty and toughness, and it is used in kitchenware, high-end furniture, musical instruments, and many other areas.
Joboji Lacquer: An introduction to the urushi lacquer of Joboji, the largest producer of domestically produced urushi
Urushi is a symbol of Japanese characteristics.
Urushi is close to people’s lives in Japan today, but it has a long history—its roots go back to about 9,000 years ago.
Urushi has long been a part of people’s day-to-day lives, through its use in utensils of various types, as construction material, and as artisanal-craft material.
However, the production volume of raw urushi is currently very low.
Joboji in Iwate Prefecture is the number-one location of urushi production in Japan, producing about 80% of domestically produced Japanese lacquer.
Meanwhile, 98% of the lacquer used in Japan is imported from abroad.
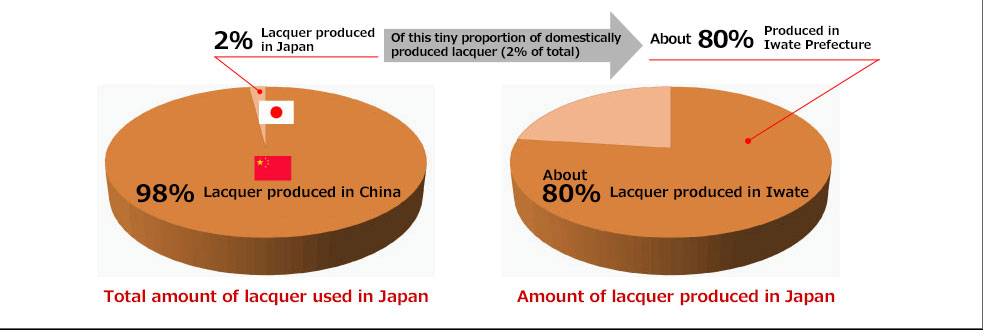
The small amount of domestically produced lacquer is produced in regions such as Iwate Prefecture, Ibaraki Prefecture, and Niigata Prefecture. Among these locations, Joboji is the only location where a team of lacquer-gathering artisans makes a coordinated effort to produce rather large amounts of lacquer.
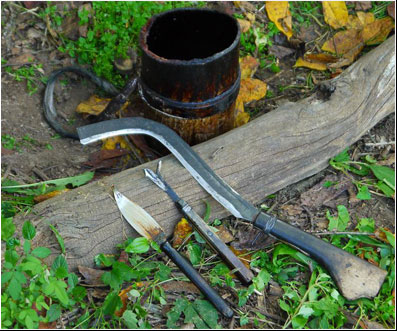
Lacquer is gathered every single day—except when it is raining—from mid-June to mid-October.
It takes about 15–20 years for an urushi tree to mature from when it is planted as a seedling.
A mature urushi tree yields no more than about 200 grams (about 7 ounces) of urushi lacquer.
After spending about six months collecting all the lacquer that a tree can yield (about 7 ounces), that tree is cut down. This is done in order to start the next cycle (i.e., growing the next urushi tree).
Here are the tools you need to gather urushi lacquer: a scythe to remove the tree’s outer bark, a special knife to cut horizontal slits into the tree, a spatula to receive the secreted lacquer, and a bucket called a “takappo” to collect the lacquer.
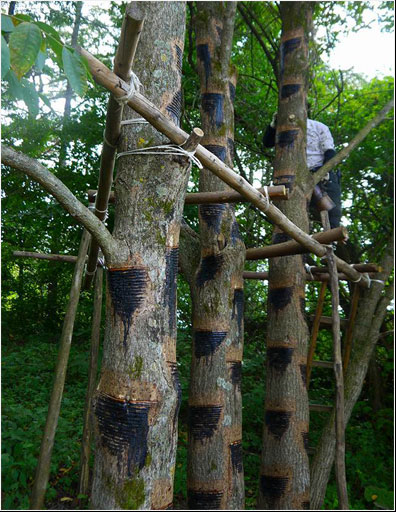
After using the scythe to remove the outer bark, the special knife is used to make about 10 small slits on the outer-bark-free surface.
The purpose of these small slits is to stimulate the tree to secrete lacquer. They also serve to indicate where the lacquer gatherer should make the second and subsequent slits.
The second slit is made in the vicinity of each of the 10 small initial slits to collect lacquer. Subsequent slits are made in the same way.
As soon as a slit is cut, the tree starts to secrete milky-white lacquer.
The gatherer receives the secreted lacquer with the spatula and transfers it to the bucket drop by drop. This routine task is carried out every day for many days.
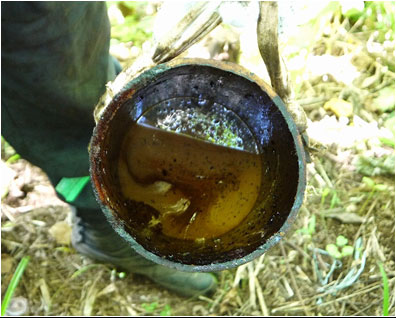
According to some theories, the word “urushi” is derived from “uruwashi,” which means beauty, or “uruoshi,” which means moisturizing.
With roots dating back about 9,000 years to the early Jomon Period in Japan, urushi lacquer boasts a long history and has created a traditional culture that is indispensable to people’s lives. However, due to economic reasons, lacquer-gathering artisans have decreased in recent years. Today, only 2% of the amount of lacquer consumed in Japan is actually produced in Japan.
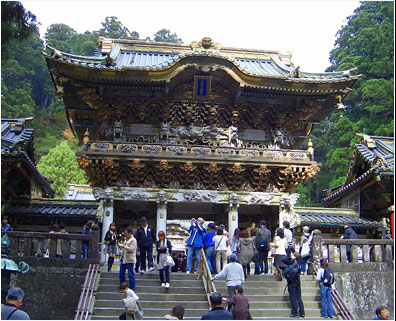
Nevertheless, Joboji Lacquer is essential not only to the day-to-day activities of lacquer artisans but also to the repairs and restorations of National Treasures and Important Cultural Properties, such as the Shrines and Temples of Nikko, including Nikko Toshogu Shrine; the Konjiki-do of Chuson-ji in Iwate Prefecture; and the Kinkaku of Rokuon-ji in Kyoto.
The buildings, lacquerware, etc. that will be used in a Japanese environment are no doubt best constructed using the urushi taken from urushi trees grown in the Japanese environment, right?
What is maki-e?
Maki-e is a uniquely Japanese artisanal craft that involves first drawing a pattern or design using lacquer on the surface of a utensil. Gold powder, silver powder, or some other kind of decoration is then sprinkled and fixed on top of the lacquered layer.
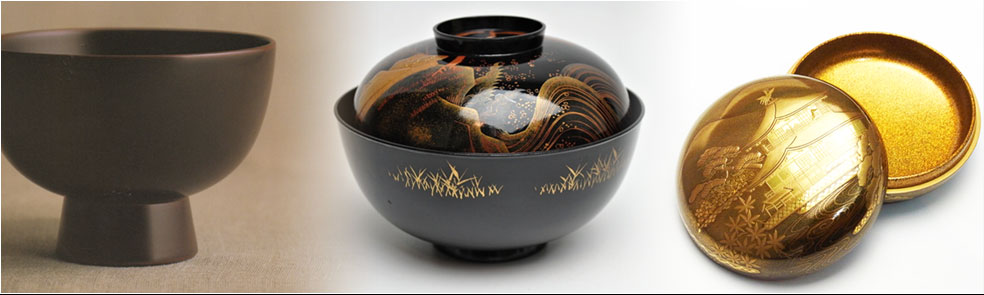
Major maki-e techniques
平蒔絵 [Hira Maki-e] |
After drawing a pattern or design with lacquer and sprinkling gold powder and/or silver powder on top of it, another layer of lacquer is applied only on top of the patterned area, which is then polished. The difference between the Hira and Togidashi Maki-e techniques is that in Togidashi Maki-e you apply the additional layer of lacquer over the entire surface of the utensil. Emerging in the late Heian Period, Hira Maki-e became the main technique used during the Momoyama Period in works such as the Kodai-ji Maki-e. |
---|---|
高蒔絵 [Taka Maki-e] |
Many layers of lacquer are added just to the patterned areas of the base lacquer so as to make them elevated, making the entire surface of the utensil more three-dimensional. |
研出蒔絵 [Togidashi Maki-e] |
On top of the sprinkled gold powder and silver powder, you apply another layer of lacquer over the entire surface of the utensil. After drying it, you polish the lacquer with charcoal in order to make the underlying maki-e layer visible again. The entire surface of the vessel becomes smooth and even after the polishing. The “makkinru” design on the Kingin-denso Kara-tachi sword, one of the Shosoin Treasures, is also a work of Togidashi Maki-e. Up until the Heian Period when pulverizing technologies had not yet been fully developed and the gold- and silver-powder particles were coarse, this was the standard maki-e technique. |
肉合蒔絵 [Shishiai Maki-e] |
This technique combines the Taka Maki-e and Togidashi Maki-e techniques. Some of the base pattern is elevated through repeated layering. Then, another layer of lacquer is applied over the entire surface. This lacquer is then polished with charcoal. The difference between this technique and the Togidashi Maki-e technique is that the surface of a Shishiai Maki-e work does not become smooth and even, even after the polishing. |
卵殻蒔絵 [Rankaku (Egg-shell) Maki-e] |
It is difficult to find colored lacquer—particularly white lacquer—that will become hard after drying and still maintain its whiteness. Therefore, when in need of white lacquer in maki-e, especially for Togidashi Maki-e, egg shells have been used as an alternative way to express whiteness. As in “raden,” small pieces of broken egg shells are arranged and fixed on a lacquered surface to create patterns. In maki-e, gold and silver powders are used in conjunction with these patterns. Maki-e that mainly uses egg shells to create the patterns is called Rankaku (which means “egg shells”) Maki-e. As for the egg shells, quail eggs are often used because their shells are thin and allow for detailed expressions. |
螺鈿蒔絵 [Raden Maki-e] |
This decorative technique involves first carving out the nacreous layer inside shellfish such as abalone, great green turban (Turbo marmoratus), and silver-lipped pearl oyster (Pinctada maxima) and making patterns or shapes out of this material. These patterns or shapes are then fitted onto the surface of the utensil you want to decorate. This is finally given a lacquer finish. Raden Maki-e thus combines the techniques of “raden” and maki-e. |